Inversor de Frequência Ideal para Motor: Escolha o Ideal
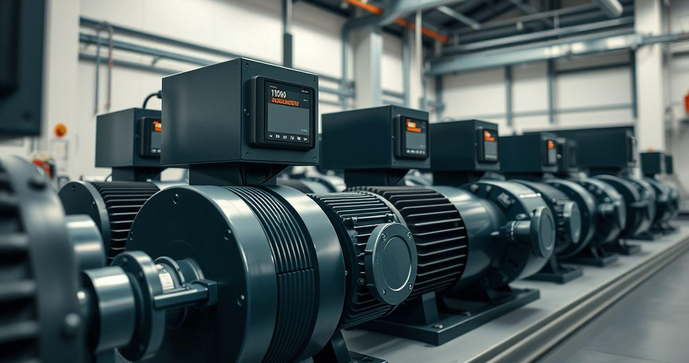
Por: Ângelo - 30 de Junho de 2025
Entendendo o que é um inversor de frequência
Um inversor de frequência é um dispositivo eletrônico que permite controlar a velocidade e o torque de motores elétricos, especialmente os de corrente alternada (CA). Ele funciona convertendo a corrente elétrica contínua (CC) de uma fonte de alimentação em corrente alternada com a frequência e tensão ajustáveis. Essa capacidade de modulação é fundamental para atender diversas aplicações industriais e automáticas.
Os inversores de frequência são utilizados em sistemas que requerem variação de velocidade de operação, como em bombas, ventiladores e compressores. Com um inversor, é possível otimizar o desempenho do motor, reduzindo o consumo de energia e o desgaste mecânico, resultando em menor necessidade de manutenção e aumento da vida útil do equipamento.
Além de proporcionar economia de energia, os inversores de frequência também permitem que os sistemas operem de maneira mais suave, evitando picos de corrente e minimizando ruídos operacionais. Isso melhora a experiência do usuário e contribui para um ambiente de trabalho mais seguro e eficiente.
Os principais componentes de um inversor incluem um retificador, um circuito de filtragem e um inversor que geram a saída de corrente alternada. O retificador converte a corrente alternada da rede elétrica em corrente contínua, enquanto o circuito de filtragem assegura um fornecimento estável. Por fim, o inversor gera uma saída de corrente alternada com a frequência desejada, permitindo o controle preciso do motor.
Em resumo, entender o funcionamento e as vantagens de um inversor de frequência é crucial para a implementação de sistemas mais eficientes e sustentáveis, promovendo economia de energia e maior controle sobre a operação dos motores.
Vantagens do uso de inversores de frequência em motores
O uso de inversores de frequência em motores elétricos oferece uma variedade de vantagens que são essenciais para a eficiência operacional e a redução de custos. Uma das principais vantagens é a economia de energia. Ao controlar a velocidade do motor, os inversores permitem que o equipamento funcione apenas na capacidade necessária, evitando o desperdício de energia em aplicações onde a velocidade máxima não é sempre necessária.
Além da economia de energia, os inversores de frequência também contribuem para a redução do desgaste mecânico do motor. Com a habilidade de regular a velocidade e o torque, o inversor minimiza os impactos de arranques e paradas bruscas, prolongando a vida útil do motor e reduzindo a necessidade de manutenção regular.
A suavidade na operação é outra característica importante. Os inversores possibilitam transições suaves de velocidade, o que reduz ruídos e vibrações durante o funcionamento. Isso é particularmente vantajoso em ambientes industriais, onde o conforto e a segurança do trabalhador são prioridades. Uma operação mais tranquila também resulta em menos danos ao equipamento e ao sistema em geral.
Além disso, a flexibilidade proporcionada por inversores de frequência permite adaptações rápidas a mudanças nas condições operacionais. Isso é crucial em ambientes de produção dinâmicos, onde a capacidade de ajustar a velocidade do motor de acordo com a demanda é uma vantagem competitiva significativa.
Por fim, os inversores de frequência podem oferecer funcionalidades adicionais, como monitoramento e diagnóstico do motor, melhorando a capacidade de manutenção preditiva. Com dados em tempo real sobre o desempenho do motor, as empresas podem identificar problemas potenciais antes que se tornem sérios, evitando paradas não programadas e mantendo a eficiência operacional.
Como selecionar o inversor de frequência ideal para seu motor
Selecionar o inversor de frequência ideal para um motor envolve considerar vários fatores que influenciam o desempenho e a eficiência do equipamento. O primeiro passo é determinar o tipo de motor que você está utilizando. Inversores diferentes são projetados para motores monofásicos ou trifásicos, e a escolha errada pode comprometer a operação do sistema.
Outro fator importante é a potência do motor. A potência do inversor deve ser compatível com a potência nominal do motor. É recomendável que o inversor tenha uma classificação de potência ligeiramente superior à do motor, para lidar com picos de carga e proteger o sistema de sobrecargas. Verifique sempre as especificações do fabricante para garantir que o inversor que você escolher suporte a carga operacional.
A faixa de frequência do inversor também deve ser considerada. Cada aplicação pode exigir uma faixa de operação específica, e é fundamental que o inversor selecionado atenda a essa faixa. Inversores com ampla faixa de frequência podem oferecer maior flexibilidade, permitindo que o motor opere em diferentes condições de carga e demanda.
Adicionalmente, o nível de controle requerido é um aspecto que não pode ser ignorado. Alguns inversores oferecem recursos avançados, como controle vetorial, que permite uma resposta mais rápida e precisa às mudanças de carga. Se sua aplicação demanda controle rigoroso de torque e velocidade, considerar um inversor com essas capacidades pode ser vantajoso.
Por último, mas não menos importante, a facilidade de instalação e configuração do inversor é um fator a ser considerado. Modelos que oferecem interfaces de programação amigáveis e suporte técnico são preferíveis para garantir que a instalação e a manutenção sejam realizadas sem complicações. A leitura do manual do usuário e a consulta aos representantes do fabricante podem fornecer informações valiosas para a seleção do inversor ideal.
Dicas para instalação de inversores de frequência
A instalação de inversores de frequência requer atenção a detalhes e ao seguimento de alguns passos fundamentais para garantir que o sistema funcione de maneira eficiente e segura. O primeiro passo crucial é escolher um local adequado para a instalação do inversor. Esse local deve ser seco, bem ventilado e livre de fontes de calor excessivo ou poeira, visto que esses fatores podem afetar o desempenho do equipamento.
Antes de iniciar a instalação, é essencial ter em mãos todas as ferramentas necessárias, além dos materiais que acompanham o inversor, como cabos e conectores. Verifique se você possui um multímetro para aferir as conexões elétricas e garantir que estão em conformidade com as especificações do fabricante. Isso ajuda a evitar erros que possam prejudicar o funcionamento do inversor.
Durante a instalação, siga rigorosamente as orientações fornecidas pelo fabricante. Consulte o manual do usuário frequentemente para assegurar que cada componente seja instalado corretamente, assim como os cabos elétricos e os fusíveis de proteção. Uma instalação inadequada pode resultar em falhas no equipamento e até riscos de segurança.
É importante também considerar a compatibilidade dos cabos utilizados com a corrente e a tensão nominal do inversor. Utilize cabos com isolamento adequado e classificado para a corrente que passará por eles. Isso garante a segurança do sistema e previne sobrecargas que podem danificar o equipamento.
Após a instalação, é fundamental realizar testes para verificar se todas as conexões estão seguras e se o inversor está funcionando adequadamente. Teste a alimentação e verifique se o motor responde corretamente às mudanças de velocidade. Qualquer sinal de anomalia deve ser investigado imediatamente para evitar danos ao sistema. Por fim, mantenha um registro da instalação e dos testes realizados, pois isso facilitará futuras manutenções e diagnósticos.
Manutenção necessária para inversores de frequência
A manutenção regular dos inversores de frequência é essencial para garantir seu funcionamento eficiente e prolongar a vida útil do equipamento. O primeiro aspecto a ser considerado é a limpeza do invólucro do inversor. Poeira e sujeira podem se acumular nas aberturas de ventilação e nos componentes internos, o que pode levar ao superaquecimento. Portanto, recomenda-se realizar a limpeza periódica com um pano seco e evitar o uso de líquidos que possam danificar os componentes eletrônicos.
Além da limpeza, é importante inspecionar as conexões elétricas regularmente. Verifique se os conectores estão firmes e se não há sinais de corrosão ou desgaste. Conexões soltas podem resultar em falhas no funcionamento do inversor e, em casos extremos, podem causar curtos-circuitos. A identificação de problemas elétricos precocemente pode evitar interrupções no funcionamento do motor.
A ventilação adequada também é fundamental na manutenção de inversores de frequência. Certifique-se de que as aberturas de ventilação estejam desobstruídas e que o equipamento não esteja exposto a temperaturas excessivas, e se necessário, instale ventiladores adicionais para melhorar a circulação de ar. Uma boa ventilação garante que os componentes eletrônicos operem dentro das temperaturas recomendadas, evitando falhas.
Outra fase importante da manutenção é a verificação dos parâmetros de configuração do inversor. É recomendável revisar as configurações de operação e comparar com as especificações do motor. Ajustes nos parâmetros, caso necessário, podem otimizar o desempenho operacional e aumentar a eficiência do sistema. Consulte o manual do fabricante para garantir que as configurações estejam corretas.
Por fim, considere a possibilidade de implementar um programa de manutenção preditiva. Isso envolve o monitoramento contínuo do desempenho do inversor e a realização de testes periódicos, que podem identificar anomalias antes que elas se tornem problemas sérios. Um registro de todas as manutenções e inspeções realizadas é valioso para manter a saúde do sistema e planejar intervenções futuras de maneira eficaz.
Soluções comuns para problemas com inversores de frequência
Problemas com inversores de frequência podem ocorrer e, quando isso acontece, é crucial ter soluções práticas à mão. Um dos problemas mais comuns é o inversor não iniciar ou não funcionar. Isso pode ser causado por falhas na fonte de alimentação, circuitos de proteção ativados ou configurações inadequadas. Para solucionar, verifique as conexões elétricas e certifique-se de que a fonte de alimentação está funcionando corretamente. Além disso, revise se os fusíveis estão intactos e se não houve ativação dos circuitos de proteção do inversor.
Outro problema frequente é a sobrecarga do motor, que pode ser indicada por uma interrupção no funcionamento do inversor. Isso pode acontecer se o motor estiver trabalhando além de sua capacidade. Nesse caso, avalie a carga conectada ao motor e considere reduzir a carga ou optar por um inversor de maior potência. Monitorar a temperatura do motor e das conexões também é recomendado para evitar danos.
Um sinal de desequilíbrio nas fases de um motor trifásico pode causar falhas de operação. Se o inversor estiver falhando por causa de desequilíbrios nas fases, verifique as tensões e correntes em cada fase. Em caso de diferenças significativas, consulte um eletricista para diagnosticar e corrigir o problema de alimentação elétrica.
Ruídos ou vibrações excessivas podem indicar problemas mecânicos no motor. Se o inversor estiver funcionando corretamente e o motor ainda fizer barulho, pode haver um desalinhamento mecânico ou necessidade de lubrificação nas partes móveis. Faça uma inspeção física do motor para diagnosticar e corrigir qualquer problema mecânico identificado.
Por último, se o inversor não estiver respondendo às configurações de controle, verifique o painel de controle e os cabos de comunicação. Problemas de mau contato, cabos danificados ou falhas no painel de controle podem impedir o funcionamento adequado. Se o problema persistir, consultar o suporte técnico do fabricante pode ser a melhor alternativa para resolver questões específicas.
Em conclusão, a implementação e o uso de inversores de frequência em motores elétricos proporcionam uma série de benefícios que vão desde a economia de energia até o aumento da vida útil do equipamento.
Compreender como selecionar o inversor adequado, realizar a instalação correta e seguir um plano de manutenção regular é fundamental para garantir um desempenho ótimo.
Os desafios que podem surgir durante o uso de inversores podem ser gerenciados com um planejamento proativo e a aplicação de soluções eficazes.
A atenção a detalhes, como a limpeza e a verificação das conexões, e o monitoramento constante podem evitar problemas mais sérios no futuro.
Investir tempo no conhecimento sobre inversores de frequência é essencial para maximizar eficiência operacional e reduzir custos ao longo do tempo.
Com as informações e práticas certas, você estará apto a aproveitar ao máximo essa tecnologia inovadora, melhorando a performance de seus motores e sistemas industriais.